Custom plastic extrusion designed to your industry needs
Custom plastic extrusion designed to your industry needs
Blog Article
Key Benefits and Factors To Consider of Executing Plastic Extrusion in Your Jobs

Understanding the Basics of Plastic Extrusion
Plastic extrusion, a staple in the manufacturing sector, is a process that entails melting raw plastic material and improving it into a continuous account. The beauty of plastic extrusion lies in its flexibility. The choice of plastic and the design of the die establish the item's attributes.
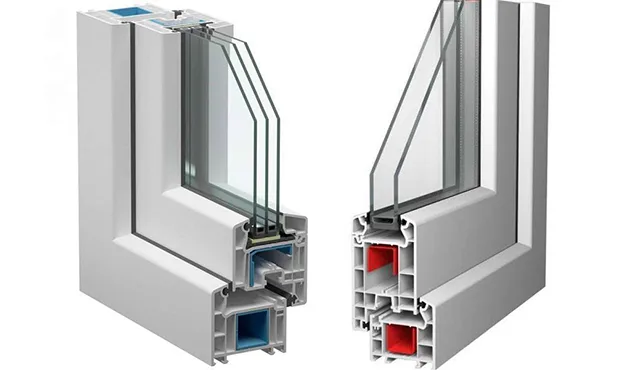
The Economic Benefit of Plastic Extrusion
The financial advantage of plastic extrusion lies predominantly in 2 locations: cost-effective material manufacturing and valuable production rates. With plastic extrusion, organizations can create high quantities of product at a reduced price compared to other approaches. The process boasts an outstanding production rate, dramatically minimizing time and further enhancing its financial practicality.
Affordable Product Manufacturing
A significant advantage of plastic extrusion is its exceptional cost-effectiveness. This production process permits for continual, high-volume manufacturing with very little waste, which translates right into reduced expenses. The raw products made use of, normally plastic pellets, are fairly cost-effective compared to various other compounds (plastic extrusion). The procedure itself requires less energy than numerous various other production approaches, better lowering prices. Furthermore, the extrusion procedure permits a high level of precision fit the plastic, minimizing the need for expensive post-production modifications or corrections. The longevity and durability of extruded plastic products typically suggest much less require for replacements, contributing to lasting savings. All these elements make plastic extrusion a highly cost-effective choice for numerous tasks, providing an appealing equilibrium between price and performance.
Beneficial Manufacturing Speeds
While maintaining the cost-effectiveness of the materials, an additional significant advantage of plastic extrusion lies in its rapid production speeds. This mix of high quality, cost-effectiveness, and speed emphasizes the considerable financial advantage of applying plastic extrusion in numerous jobs.
Adaptability and Personalization: The Strengths of Plastic Extrusion
One of the noticeable strengths of plastic extrusion hinges on its versatility and customization potential. These qualities unlock to limitless design opportunities, giving suppliers the capability to customize items to certain requirements. This enhanced degree of modification not just enhances item performance yet additionally dramatically improves item individuality.
Unrestricted Layout Opportunities
Plastic extrusion shines in its ability to supply almost unlimited layout opportunities. This approach gives flexibility to create intricate shapes and intricate accounts, an accomplishment difficult to accomplish with other construction strategies. Owing to the fluid nature of liquified plastic, the process is adaptable enough to generate a diverse array of dimensions, kinds, and dimensions. The plastic can be manipulated to match one-of-a-kind specs, permitting the manufacturing of tailored geometries and conference particular client demands. Plastic extrusion can take care of a range of plastic types, expanding its application range. This adaptable technique, as a result, offers a vast array of industries from building to automotive, packaging to electronics, and past. With plastic extrusion, the layout opportunities are practically unlimited.
Boosting Product Individuality
The convenience of plastic extrusion can substantially boost item individuality. This process allows developers to try out various shapes, sizes, and colors, giving them the freedom to create distinct items that stand out in the marketplace. It is this customization that offers an unique identification to every item, differentiating it from its competitors.
In enhancement to its aesthetic advantages, the customizability of plastic extrusion likewise provides practical advantages. Therefore, plastic extrusion not just increases product individuality but also its utility and marketability.
Layout Limitations in Plastic Extrusion: What You Need to Know
Just how can design restrictions possibly affect the process of plastic extrusion? While plastic extrusion is versatile, layout restrictions can reduce its benefits. Particular complex layouts may not be viable due to the limitations of the extrusion process, potentially limiting the development of intricate profiles. The process is much less appropriate for hollow or multi-chambered frameworks. Furthermore, the extrusion process may not always give the wanted surface area coating, particularly for those needing high gloss or optical clarity. Product choice can also present difficulties, as not all polymers appropriate for extrusion. High-temperature immune plastics, for instance, may offer troubles. Understanding these restrictions is essential for effective implementation of plastic extrusion in your tasks. plastic extrusion.
Reviewing the Ecological Impact of Plastic Extrusion
While understanding layout constraints is a substantial facet of plastic extrusion, it is similarly crucial to consider its ecological implications. The procedure of plastic extrusion entails melting plastic materials, possibly releasing harmful gases into the environment. Additionally, the resulting products are usually non-biodegradable, adding to landfill waste. Nonetheless, advancements in modern technology have permitted more environmentally-friendly techniques. For example, using recycled plastic products in the extrusion process can decrease ecological influence. In addition, creating naturally degradable plastic options can assist alleviate waste issues. Reviewing these environmental variables is essential when carrying out plastic extrusion projects, ensuring an equilibrium between effectiveness, cost-effectiveness, and environmental duty.
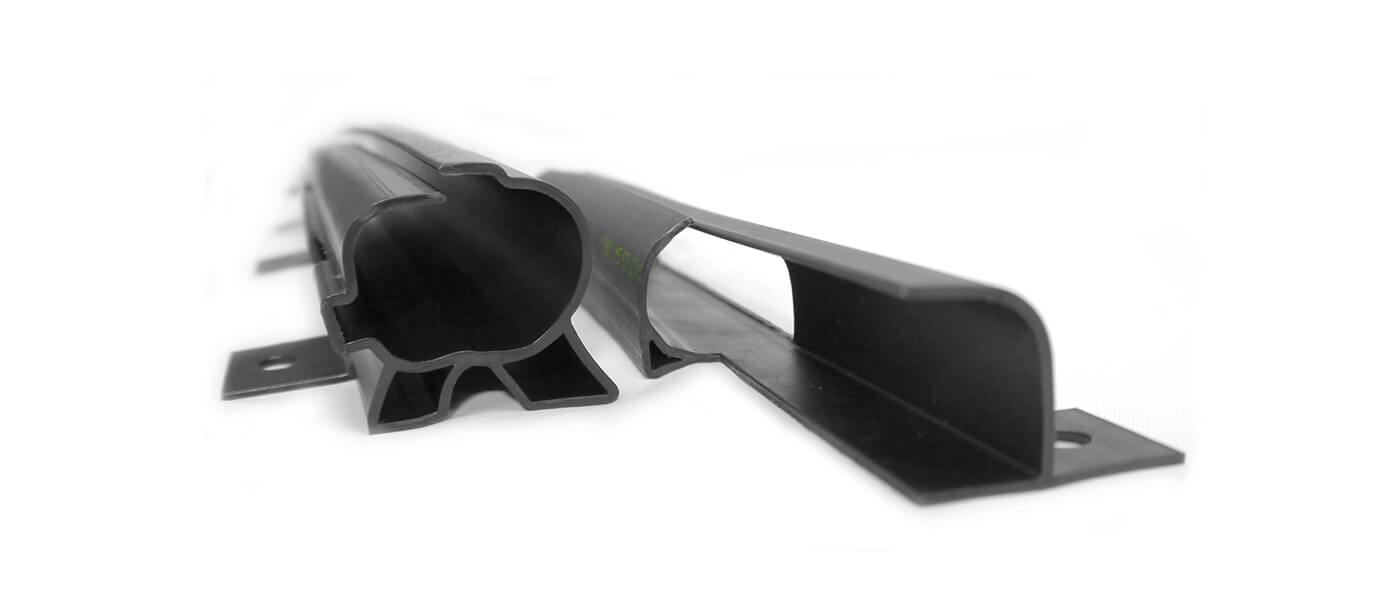
Case Research Study: Successful Projects Utilizing Plastic Extrusion
Success tales in the field of plastic extrusion are plentiful, demonstrating both the versatility and effectiveness of this production process. One noteworthy example is the development of PVC pipes made use of in modern-day plumbing. This process entails melting plastic and forming it right into a continuous tube, providing substantial price and durability benefits. anonymous An additional effective case is the production of plastic film for product packaging and farming. With extrusion, suppliers can create highly personalized, thin, and durable check it out films. Automotive sectors likewise profit, using extruded plastic for components like trim or seals, improving lorry long life. These instances highlight plastic extrusion's critical duty in different sectors, vouching for its versatility, cost-effectiveness, and trustworthy result.
Final thought
In verdict, plastic extrusion uses a cost-effective and efficient approach for creating intricate shapes with minimal waste. While it gives countless advantages such as cost-effectiveness and convenience, it's crucial to think about potential style limitations and environmental effects. Executing recycled or eco-friendly products can minimize these problems, improving sustainability. Incorporating plastic extrusion into jobs can cause successful results, as confirmed by countless study.
Plastic extrusion, a staple in the production industry, is a procedure that entails melting raw plastic material and Get the facts reshaping it right into a constant account. Plastic extrusion can manage a selection of plastic kinds, broadening its application range.How can develop constraints possibly impact the procedure of plastic extrusion? The procedure of plastic extrusion involves melting plastic materials, potentially launching hazardous gases right into the environment. Utilizing recycled plastic materials in the extrusion procedure can minimize environmental impact.
Report this page